SPC (Statistisk Processkontrol) er et afgørende værktøj i waferfremstillingsprocessen og bruges til at overvåge, kontrollere og forbedre stabiliteten i forskellige trin i fremstillingen.
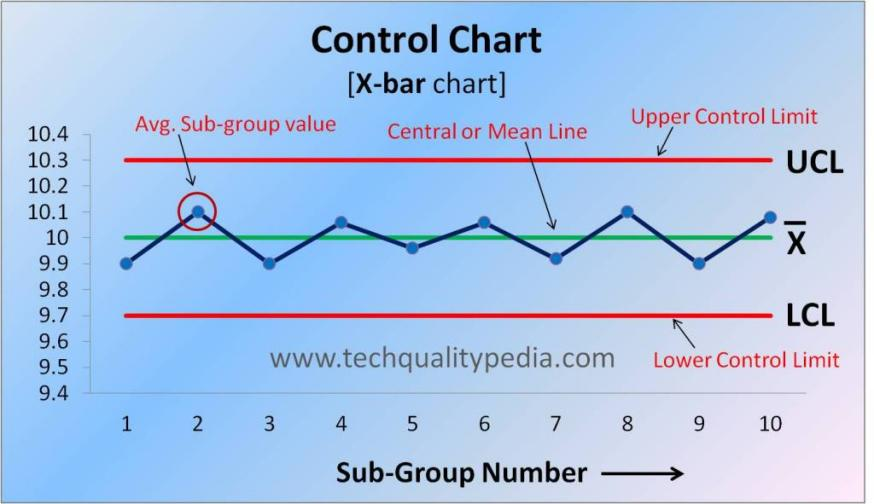
1. Oversigt over SPC-systemet
SPC er en metode, der bruger statistiske teknikker til at overvåge og kontrollere fremstillingsprocesser. Dens kernefunktion er at opdage anomalier i produktionsprocessen ved at indsamle og analysere realtidsdata, hvilket hjælper ingeniører med at foretage rettidige justeringer og beslutninger. Målet med SPC er at reducere variation i produktionsprocessen og sikre, at produktkvaliteten forbliver stabil og opfylder specifikationerne.
SPC bruges i ætseprocessen til at:
Overvåg kritiske udstyrsparametre (f.eks. ætsehastighed, RF-effekt, kammertryk, temperatur osv.)
Analyser vigtige produktkvalitetsindikatorer (f.eks. linjebredde, ætsningsdybde, kanteruhed osv.)
Ved at overvåge disse parametre kan ingeniører opdage tendenser, der indikerer forringelse af udstyrets ydeevne eller afvigelser i produktionsprocessen, og dermed reducere skrotprocenterne.
2. Grundlæggende komponenter i SPC-systemet
SPC-systemet er sammensat af flere nøglemoduler:
Dataindsamlingsmodul: Indsamler realtidsdata fra udstyr og procesflow (f.eks. via FDC, EES-systemer) og registrerer vigtige parametre og produktionsresultater.
Kontroldiagrammodul: Bruger statistiske kontroldiagrammer (f.eks. X-bar-diagram, R-diagram, Cp/Cpk-diagram) til at visualisere processtabilitet og hjælpe med at bestemme, om processen er under kontrol.
Alarmsystem: Udløser alarmer, når kritiske parametre overstiger kontrolgrænser eller viser tendensændringer, hvilket får ingeniører til at handle.
Analyse- og rapporteringsmodul: Analyserer den grundlæggende årsag til anomalier baseret på SPC-diagrammer og genererer regelmæssigt præstationsrapporter for processen og udstyret.
3. Detaljeret forklaring af kontroldiagrammer i SPC
Kontroldiagrammer er et af de mest anvendte værktøjer i SPC, der hjælper med at skelne mellem "normal variation" (forårsaget af naturlige procesvariationer) og "unormal variation" (forårsaget af udstyrsfejl eller procesafvigelser). Almindelige kontroldiagrammer omfatter:
X-Bar- og R-diagrammer: Bruges til at overvåge gennemsnittet og intervallet inden for produktionsbatcher for at observere, om processen er stabil.
Cp- og Cpk-indekser: Bruges til at måle proceskapacitet, dvs. om procesoutputtet konsekvent kan opfylde specifikationskravene. Cp måler den potentielle kapacitet, mens Cpk tager hensyn til procescentrets afvigelse fra specifikationsgrænserne.
For eksempel kan du i ætseprocessen overvåge parametre som ætsehastighed og overfladeruhed. Hvis ætsehastigheden for et bestemt stykke udstyr overstiger kontrolgrænsen, kan du bruge kontroldiagrammer til at bestemme, om dette er en naturlig variation eller en indikation af en fejl i udstyret.
4. Anvendelse af SPC i ætseudstyr
I ætseprocessen er det afgørende at kontrollere udstyrets parametre, og SPC hjælper med at forbedre processtabiliteten på følgende måder:
Overvågning af udstyrstilstand: Systemer som FDC indsamler realtidsdata om nøgleparametre for ætseudstyr (f.eks. RF-effekt, gasflow) og kombinerer disse data med SPC-kontroldiagrammer for at opdage potentielle udstyrsproblemer. Hvis du f.eks. ser, at RF-effekten på et kontroldiagram gradvist afviger fra den indstillede værdi, kan du træffe tidlige foranstaltninger til justering eller vedligeholdelse for at undgå at påvirke produktkvaliteten.
Overvågning af produktkvalitet: Du kan også indtaste vigtige produktkvalitetsparametre (f.eks. ætsedybde, linjebredde) i SPC-systemet for at overvåge deres stabilitet. Hvis nogle kritiske produktindikatorer gradvist afviger fra målværdierne, vil SPC-systemet udstede en alarm, der angiver, at procesjusteringer er nødvendige.
Forebyggende vedligeholdelse (PM): SPC kan hjælpe med at optimere den forebyggende vedligeholdelsescyklus for udstyr. Ved at analysere langsigtede data om udstyrets ydeevne og procesresultater kan du bestemme det optimale tidspunkt for udstyrets vedligeholdelse. For eksempel kan du ved at overvåge RF-effekt og ESC-levetid bestemme, hvornår rengøring eller udskiftning af komponenter er nødvendig, hvilket reducerer udstyrsfejl og produktionsnedetid.
5. Daglige brugstips til SPC-systemet
Når SPC-systemet anvendes i den daglige drift, kan følgende trin følges:
Definer nøglekontrolparametre (KPI): Identificer de vigtigste parametre i produktionsprocessen, og inkluder dem i SPC-overvågningen. Disse parametre bør være tæt relateret til produktkvalitet og udstyrets ydeevne.
Indstil kontrolgrænser og alarmgrænser: Baseret på historiske data og proceskrav skal du indstille rimelige kontrolgrænser og alarmgrænser for hver parameter. Kontrolgrænser er normalt indstillet til ±3σ (standardafvigelser), mens alarmgrænser er baseret på de specifikke forhold i processen og udstyret.
Kontinuerlig overvågning og analyse: Gennemgå regelmæssigt SPC-kontroldiagrammer for at analysere datatendenser og variationer. Hvis nogle parametre overstiger kontrolgrænserne, er der behov for øjeblikkelig handling, såsom justering af udstyrsparametre eller udførelse af vedligeholdelse af udstyr.
Håndtering af abnormiteter og analyse af rodårsager: Når en abnormitet opstår, registrerer SPC-systemet detaljerede oplysninger om hændelsen. Du skal fejlfinde og analysere den grundlæggende årsag til abnormiteten baseret på disse oplysninger. Det er ofte muligt at kombinere data fra FDC-systemer, EES-systemer osv. for at analysere, om problemet skyldes udstyrsfejl, procesafvigelse eller eksterne miljøfaktorer.
Kontinuerlig forbedring: Brug de historiske data, der er registreret af SPC-systemet, til at identificere svage punkter i processen og foreslå forbedringsplaner. For eksempel, i ætseprocessen, analysere virkningen af ESC-levetid og rengøringsmetoder på udstyrets vedligeholdelsescyklusser og løbende optimere udstyrets driftsparametre.
6. Praktisk anvendelsescase
Som et praktisk eksempel, antag at du er ansvarlig for ætseudstyret E-MAX, og kammerkatoden oplever for tidlig slitage, hvilket fører til en stigning i D0-værdierne (BARC-defekt). Ved at overvåge RF-effekten og ætsehastigheden via SPC-systemet bemærker du en tendens, hvor disse parametre gradvist afviger fra deres indstillede værdier. Efter at en SPC-alarm er udløst, kombinerer du data fra FDC-systemet og bestemmer, at problemet skyldes ustabil temperaturkontrol inde i kammeret. Du implementerer derefter nye rengøringsmetoder og vedligeholdelsesstrategier, hvilket i sidste ende reducerer D0-værdien fra 4,3 til 2,4 og dermed forbedrer produktkvaliteten.
7. I XINKEHUI kan du få.
Hos XINKEHUI kan du opnå den perfekte wafer, uanset om det er en siliciumwafer eller en SiC-wafer. Vi specialiserer os i at levere wafere af højeste kvalitet til forskellige industrier med fokus på præcision og ydeevne.
(siliciumwafer)
Vores siliciumwafere er fremstillet med overlegen renhed og ensartethed, hvilket sikrer fremragende elektriske egenskaber til dine halvlederbehov.
Til mere krævende applikationer tilbyder vores SiC-wafere enestående varmeledningsevne og højere effekteffektivitet, hvilket er ideelt til effektelektronik og miljøer med høje temperaturer.
(SiC-wafer)
Med XINKEHUI får du banebrydende teknologi og pålidelig support, der garanterer wafere, der opfylder de højeste branchestandarder. Vælg os for at få perfektion til dine wafere!
Opslagstidspunkt: 16. oktober 2024