Wafer dicing-teknologi, som et kritisk trin i halvlederfremstillingsprocessen, er direkte knyttet til chips ydeevne, udbytte og produktionsomkostninger.
#01 Baggrund og betydning af wafer-udskæring
1.1 Definition af wafer-udskæring
Wafer dicing (også kendt som scribing) er et vigtigt trin i halvlederfremstilling, der har til formål at opdele forarbejdede wafers i flere individuelle dies. Disse dies indeholder typisk komplet kredsløbsfunktionalitet og er de kernekomponenter, der i sidste ende bruges i produktionen af elektroniske enheder. Efterhånden som chipdesign bliver mere komplekse, og dimensionerne fortsætter med at krympe, bliver præcisions- og effektivitetskravene til wafer dicing-teknologi stadig strengere.
I praksis bruger wafer-udskæring typisk højpræcisionsværktøjer såsom diamantklinger for at sikre, at hver matrice forbliver intakt og fuldt funktionel. Nøgletrin omfatter forberedelse før skæring, præcis kontrol under skæreprocessen og kvalitetsinspektion efter skæring.
Før skæring skal waferen markeres og placeres for at sikre nøjagtige skærebaner. Under skæringen skal parametre som værktøjstryk og hastighed kontrolleres nøje for at forhindre beskadigelse af waferen. Efter skæringen udføres omfattende kvalitetsinspektioner for at sikre, at hver chip opfylder ydeevnestandarderne.
De grundlæggende principper for wafer-dicingteknologi omfatter ikke kun valg af skæreudstyr og indstilling af procesparametre, men også indflydelsen af materialernes mekaniske egenskaber og karakteristika på skærekvaliteten. For eksempel er lav-k dielektriske siliciumwafere på grund af deres ringere mekaniske egenskaber meget modtagelige for spændingskoncentration under skæring, hvilket fører til fejl såsom afskalning og revner. Den lave hårdhed og sprødhed af lav-k-materialer gør dem mere tilbøjelige til strukturelle skader under mekanisk kraft eller termisk belastning, især under skæring. Kontakten mellem værktøjet og waferoverfladen kombineret med høje temperaturer kan yderligere forværre spændingskoncentrationen.
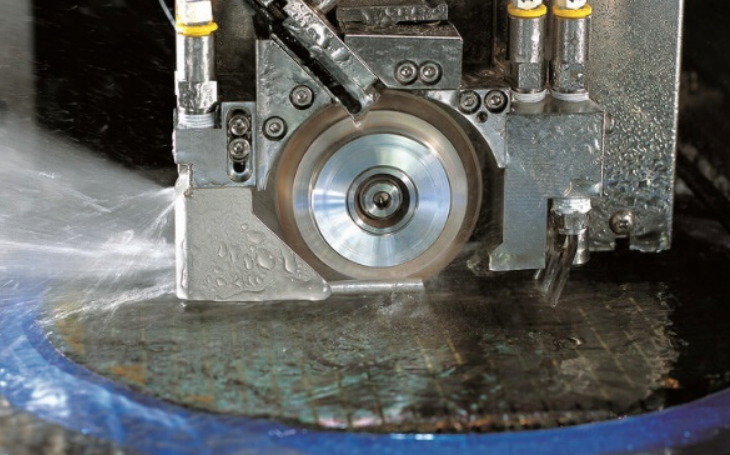
Med fremskridt inden for materialevidenskab er wafer-dicing-teknologien blevet udvidet ud over traditionelle siliciumbaserede halvledere til også at omfatte nye materialer som galliumnitrid (GaN). Disse nye materialer stiller på grund af deres hårdhed og strukturelle egenskaber nye udfordringer for dicing-processer og kræver yderligere forbedringer af skæreværktøjer og -teknikker.
Som en kritisk proces i halvlederindustrien fortsætter wafer dicing med at blive optimeret som reaktion på udviklende krav og teknologiske fremskridt, hvilket lægger grunden til fremtidens mikroelektronik- og integrerede kredsløbsteknologier.
Forbedringer inden for wafer-dicingteknologi går ud over udviklingen af hjælpematerialer og værktøjer. De omfatter også procesoptimering, forbedringer i udstyrets ydeevne og præcis kontrol af dicingparametre. Disse fremskridt har til formål at sikre høj præcision, effektivitet og stabilitet i wafer-dicingprocessen og dermed imødekomme halvlederindustriens behov for mindre dimensioner, højere integration og mere komplekse chipstrukturer.
forbedringsområde | Specifikke foranstaltninger | Effekter |
Procesoptimering | - Forbedre de indledende forberedelser, såsom mere præcis waferpositionering og stiplanlægning. | - Reducer skærefejl og forbedrer stabiliteten. |
- Minimer skærefejl og forbedrer stabiliteten. | - Indfør realtidsovervågnings- og feedbackmekanismer til at justere værktøjstryk, hastighed og temperatur. | |
- Reducer waferbrudsrater og forbedrer chipkvaliteten. | ||
Forbedring af udstyrsydelse | - Anvende højpræcisionsmekaniske systemer og avanceret automatiseringsstyringsteknologi. | - Forbedr skærepræcisionen og reducer materialespild. |
- Introducere laserskæreteknologi, der er egnet til wafere med høj hårdhedsgrad. | - Forbedr produktionseffektiviteten og reducer manuelle fejl. | |
- Øg udstyrsautomatiseringen til automatisk overvågning og justeringer. | ||
Præcis parameterkontrol | - Finjuster parametre som skæredybde, hastighed, værktøjstype og kølemetoder. | - Sikre chipens integritet og elektrisk ydeevne. |
- Tilpas parametre baseret på wafermateriale, tykkelse og struktur. | - Øg udbyttet, reducer materialespild og sænk produktionsomkostningerne. | |
Strategisk betydning | - Løbende udforske nye teknologiske veje, optimere processer og forbedre udstyrets kapacitet for at imødekomme markedets krav. | - Forbedre udbyttet og ydeevnen ved chipproduktion, understøtte udviklingen af nye materialer og avancerede chipdesigns. |
1.2 Vigtigheden af vaffelskæring
Wafer dicing spiller en afgørende rolle i halvlederproduktionsprocessen og påvirker direkte de efterfølgende trin samt kvaliteten og ydeevnen af det endelige produkt. Dens betydning kan beskrives som følger:
For det første er nøjagtigheden og ensartetheden af dicing afgørende for at sikre chips udbytte og pålidelighed. Under fremstillingen gennemgår wafere flere behandlingstrin for at danne adskillige komplicerede kredsløbsstrukturer, som skal opdeles præcist i individuelle chips (dies). Hvis der er betydelige fejl i justering eller skæring under dicingprocessen, kan kredsløbene blive beskadiget, hvilket påvirker chippens funktionalitet og pålidelighed. Derfor sikrer højpræcisions dicingteknologi ikke kun integriteten af hver chip, men forhindrer også skader på interne kredsløb, hvilket forbedrer det samlede udbytte.
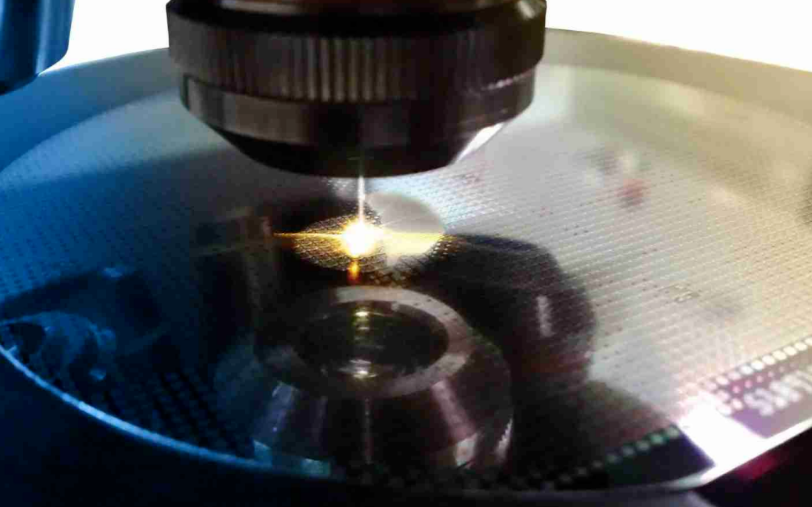
For det andet har wafer-dicing en betydelig indflydelse på produktionseffektivitet og omkostningskontrol. Som et afgørende trin i fremstillingsprocessen påvirker dets effektivitet direkte fremskridtet i de efterfølgende trin. Ved at optimere dicing-processen, øge automatiseringsniveauet og forbedre skærehastighederne kan den samlede produktionseffektivitet forbedres betydeligt.
På den anden side er materialespild under udskæring en kritisk faktor i omkostningsstyringen. Brugen af avancerede udskæringsteknologier reducerer ikke kun unødvendige materialetab under skæreprocessen, men øger også waferudnyttelsen og dermed sænker produktionsomkostningerne.
Med fremskridt inden for halvlederteknologi fortsætter waferdiametrene med at stige, og kredsløbstæthederne stiger tilsvarende, hvilket stiller højere krav til dicing-teknologi. Større wafere kræver mere præcis kontrol af skærebaner, især i områder med høj kredsløbstæthed, hvor selv mindre afvigelser kan gøre flere chips defekte. Derudover involverer større wafere flere skærelinjer og mere komplekse procestrin, hvilket nødvendiggør yderligere forbedringer i præcisionen, konsistensen og effektiviteten af dicing-teknologier for at imødekomme disse udfordringer.
1.3 Wafer-terningproces
Wafer-udskæringsprocessen omfatter alle trin fra forberedelsesfasen til den endelige kvalitetskontrol, hvor hvert trin er afgørende for at sikre kvaliteten og ydeevnen af de ternskårne chips. Nedenfor er en detaljeret forklaring af hver fase.
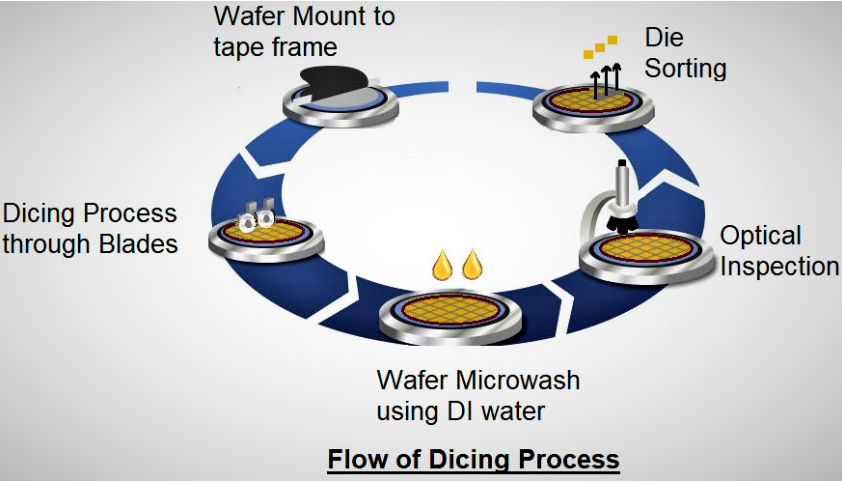
Fase | Detaljeret beskrivelse |
Forberedelsesfase | -Rengøring af vaflerBrug vand med høj renhed og specialiserede rengøringsmidler kombineret med ultralyds- eller mekanisk skrubning for at fjerne urenheder, partikler og forurenende stoffer og sikre en ren overflade. -Præcis positioneringBrug højpræcisionsudstyr til at sikre, at waferen er nøjagtigt opdelt langs de designede skærebaner. -WaferfikseringFastgør waferen på en taperamme for at opretholde stabilitet under skæring og forhindre skader fra vibrationer eller bevægelse. |
Skærefase | -KnivskæringBrug diamantbelagte klinger med høj hastighed til fysisk skæring, velegnede til siliciumbaserede materialer og omkostningseffektive. -LaserudskæringBrug højenergilaserstråler til berøringsfri skæring, ideel til sprøde eller hårde materialer som galliumnitrid, hvilket giver højere præcision og mindre materialetab. -Nye teknologierIntroduktion af laser- og plasmaskæreteknologier for yderligere at forbedre effektivitet og præcision, samtidig med at varmepåvirkede zoner minimeres. |
Rengøringsfase | - Brug deioniseret vand (DI-vand) og specialiserede rengøringsmidler kombineret med ultralyds- eller sprayrengøring til at fjerne snavs og støv, der genereres under skæring, og forhindre, at rester påvirker efterfølgende processer eller spånens elektriske ydeevne. - Højrent deioniseret vand undgår at introducere nye forurenende stoffer og sikrer et rent wafermiljø. |
Inspektionsfase | -Optisk inspektionBrug optiske detektionssystemer kombineret med AI-algoritmer til hurtigt at identificere defekter, sikre at der ikke er revner eller afskalninger i de hakkede spåner, forbedre inspektionseffektiviteten og reducere menneskelige fejl. -DimensionsmålingBekræft, at chippens dimensioner opfylder designspecifikationerne. -Elektrisk ydeevnetestningSørg for, at den elektriske ydeevne af kritiske chips opfylder standarderne, hvilket garanterer pålidelighed i efterfølgende applikationer. |
Sorteringsfase | - Brug robotarme eller vakuumsugekopper til at adskille kvalificerede chips fra taperammen og sortere dem automatisk baseret på ydeevne, hvilket sikrer produktionseffektivitet og fleksibilitet, samtidig med at præcisionen forbedres. |
Waferskæringsprocessen involverer rengøring, positionering, skæring, rengøring, inspektion og sortering af wafere, hvor hvert trin er kritisk. Med fremskridt inden for automatisering, laserskæring og AI-inspektionsteknologier kan moderne waferskæresystemer opnå højere præcision, hastighed og lavere materialetab. I fremtiden vil nye skæreteknologier som laser og plasma gradvist erstatte traditionel bladskæring for at imødekomme behovene i stadig mere komplekse chipdesigns, hvilket yderligere driver udviklingen af halvlederfremstillingsprocesser.
Waferskæringsteknologi og dens principper
Billedet illustrerer tre almindelige teknologier til waferskæring:Knivskæring,Laserudskæring, ogPlasma-udskæringNedenfor er en detaljeret analyse og supplerende forklaring af disse tre teknikker:
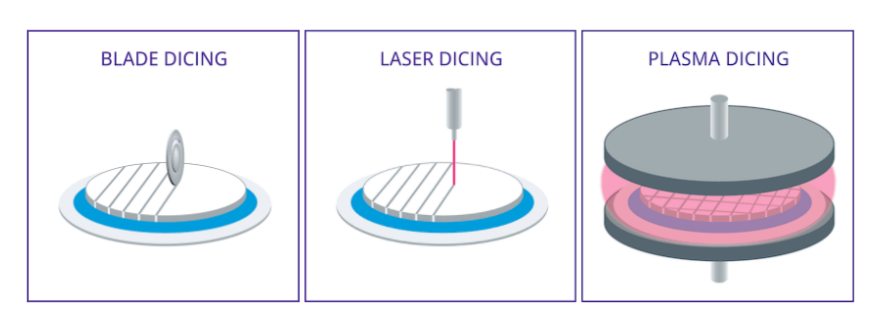
I halvlederfremstilling er waferskæring et afgørende trin, der kræver valg af den passende skæremetode baseret på waferens tykkelse. Det første trin er at bestemme waferens tykkelse. Hvis wafertykkelsen overstiger 100 mikron, kan blade dicing vælges som skæremetode. Hvis blade dicing ikke er egnet, kan fraktur-dicing-metoden anvendes, som omfatter både ridseskæring og blade dicing-teknikker.
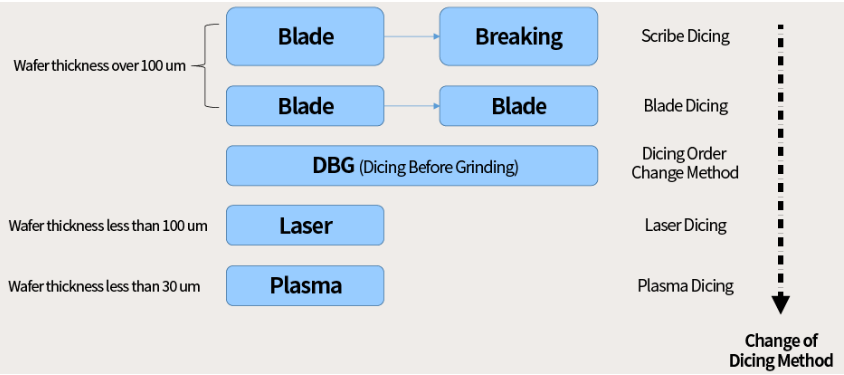
Når wafertykkelsen er mellem 30 og 100 mikron, anbefales DBG-metoden (Dice Before Grinding). I dette tilfælde kan man vælge at ridse, skære med klinge eller justere skæresekvensen efter behov for at opnå de bedste resultater.
For ultratynde wafere med en tykkelse på mindre end 30 mikron bliver laserskæring den foretrukne metode på grund af dens evne til at skære tynde wafere præcist uden at forårsage for stor skade. Hvis laserskæring ikke kan opfylde specifikke krav, kan plasmaskæring bruges som et alternativ. Dette flowdiagram giver en klar beslutningsproces for at sikre, at den mest passende waferskæreteknologi vælges under forskellige tykkelsesforhold.
2.1 Mekanisk skæreteknologi
Mekanisk skæreteknologi er den traditionelle metode inden for wafer-udskæring. Kerneprincippet er at bruge en højhastighedsroterende diamantslibeskive som skæreværktøj til at skære waferen. Nøgleudstyret omfatter en luftlejet spindel, der driver diamantslibeskiveværktøjet med høje hastigheder for at udføre præcis skæring eller sporskæring langs en foruddefineret skærebane. Denne teknologi er meget udbredt i industrien på grund af dens lave omkostninger, høje effektivitet og brede anvendelighed.
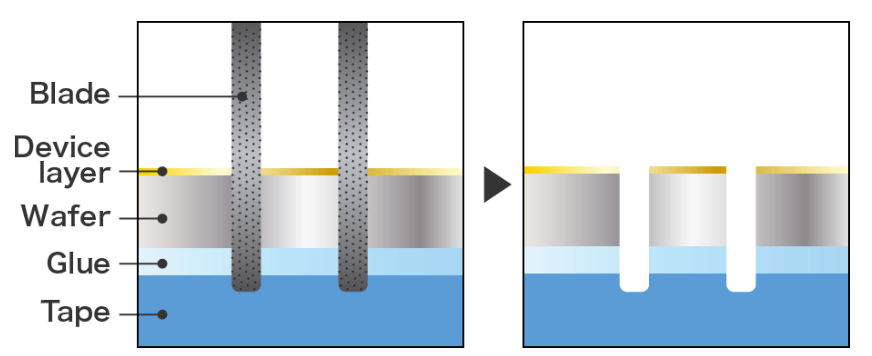
Fordele
Den høje hårdhed og slidstyrke ved diamantslibeskiveværktøjer gør det muligt for mekanisk skæreteknologi at tilpasse sig skærebehovene i forskellige wafermaterialer, uanset om det er traditionelle siliciumbaserede materialer eller nyere sammensatte halvledere. Dens betjening er enkel med relativt lave tekniske krav, hvilket yderligere fremmer dens popularitet i masseproduktion. Derudover har mekanisk skæring mere kontrollerbare omkostninger sammenlignet med andre skæremetoder som laserskæring, hvilket gør den velegnet til produktionsbehov i store mængder.
Begrænsninger
Trods sine mange fordele har mekanisk skæreteknologi også begrænsninger. For det første er skærepræcisionen relativt begrænset på grund af den fysiske kontakt mellem værktøjet og waferen, hvilket ofte fører til dimensionelle afvigelser, der kan påvirke nøjagtigheden af den efterfølgende chippakning og testning. For det andet kan defekter som afskalning og revner let opstå under den mekaniske skæreproces, hvilket ikke kun påvirker udbyttet, men også kan have en negativ indvirkning på chipsenes pålidelighed og levetid. Den mekaniske stressinducerede skade er særligt skadelig for fremstilling af chip med høj densitet, især ved skæring af sprøde materialer, hvor disse problemer er mere fremtrædende.
Teknologiske forbedringer
For at overvinde disse begrænsninger optimerer forskere løbende den mekaniske skæreproces. Vigtige forbedringer omfatter forbedring af design og materialevalg af slibeskiver for at forbedre skærepræcision og holdbarhed. Derudover har optimering af det strukturelle design og kontrolsystemerne i skæreudstyr yderligere forbedret stabiliteten og automatiseringen af skæreprocessen. Disse fremskridt reducerer fejl forårsaget af menneskelige operationer og forbedrer ensartetheden af snittene. Introduktionen af avancerede inspektions- og kvalitetskontrolteknologier til realtidsovervågning af anomalier under skæreprocessen har også forbedret skærepålidelighed og udbytte betydeligt.
Fremtidig udvikling og nye teknologier
Selvom mekanisk skæreteknologi stadig indtager en betydelig plads inden for waferskæring, udvikler nye skæreteknologier sig hurtigt i takt med at halvlederprocesser udvikler sig. For eksempel giver anvendelsen af termisk laserskæringsteknologi nye løsninger på præcisions- og defektproblemer ved mekanisk skæring. Denne berøringsfri skæremetode reducerer den fysiske belastning på waferen, hvilket reducerer forekomsten af afskalning og revner betydeligt, især ved skæring af mere sprøde materialer. I fremtiden vil integrationen af mekanisk skæreteknologi med nye skæreteknikker give halvlederproduktion flere muligheder og fleksibilitet, hvilket yderligere forbedrer produktionseffektiviteten og chipkvaliteten.
Afslutningsvis kan man sige, at selvom mekanisk skæreteknologi har visse ulemper, gør løbende teknologiske forbedringer og dens integration med nye skæreteknikker det muligt for den stadig at spille en vigtig rolle i halvlederproduktion og opretholde sin konkurrenceevne i fremtidige processer.
2.2 Laserskæringsteknologi
Laserskæringsteknologi, som en ny metode inden for waferskæring, har gradvist fået udbredt opmærksomhed i halvlederindustrien på grund af dens høje præcision, mangel på mekanisk kontaktskade og hurtige skæreegenskaber. Denne teknologi bruger laserstrålens høje energitæthed og fokuseringsevne til at skabe en lille varmepåvirket zone på wafermaterialets overflade. Når laserstrålen påføres waferen, forårsager den genererede termiske spænding, at materialet brister på det angivne sted, hvilket opnår præcis skæring.
Fordele ved laserskæreteknologi
• Høj præcisionLaserstrålens præcise positioneringskapacitet muliggør skærepræcision på mikron- eller endda nanometerniveau og opfylder kravene til moderne højpræcisions- og højdensitetsproduktion af integrerede kredsløb.
• Ingen mekanisk kontaktLaserskæring undgår fysisk kontakt med waferen, hvilket forhindrer almindelige problemer ved mekanisk skæring, såsom afskalning og revner, hvilket forbedrer chipsenes udbytte og pålidelighed betydeligt.
• Hurtig skærehastighedDen høje hastighed ved laserskæring bidrager til øget produktionseffektivitet, hvilket gør den særligt velegnet til storskala produktion med høj hastighed.
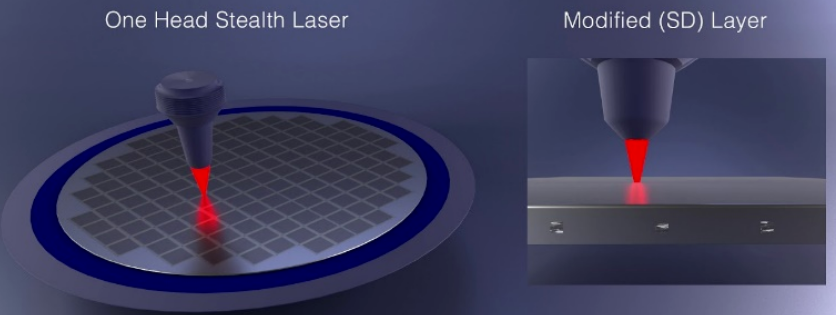
Udfordringer
• Høje udstyrsomkostningerDen indledende investering i laserskæreudstyr er høj, hvilket sætter et økonomisk pres, især for små og mellemstore produktionsvirksomheder.
• Kompleks processtyringLaserskæring kræver præcis kontrol af flere parametre, herunder energitæthed, fokusposition og skærehastighed, hvilket gør processen kompleks.
• Problemer med varmepåvirkede zonerSelvom laserskærings berøringsfri natur reducerer mekanisk skade, kan den termiske belastning forårsaget af den varmepåvirkede zone (HAZ) have en negativ indvirkning på wafermaterialets egenskaber. Yderligere optimering af processen er nødvendig for at minimere denne effekt.
Teknologiske forbedringsretninger
For at imødegå disse udfordringer fokuserer forskere på at sænke udstyrsomkostningerne, forbedre skæreeffektiviteten og optimere procesflowet.
• Effektive lasere og optiske systemerVed at udvikle mere effektive lasere og avancerede optiske systemer er det muligt at sænke udstyrsomkostningerne, samtidig med at skærepræcisionen og -hastigheden forbedres.
• Optimering af procesparametreDer udføres dybdegående forskning i interaktionen mellem lasere og wafermaterialer for at forbedre processer, der reducerer den varmepåvirkede zone og dermed forbedrer skærekvaliteten.
• Intelligente styresystemerUdviklingen af intelligente styringsteknologier har til formål at automatisere og optimere laserskæreprocessen og dermed forbedre dens stabilitet og ensartethed.
Laserskæringsteknologi er særligt effektiv i ultratynde wafere og højpræcisionsskæringsscenarier. Efterhånden som waferstørrelserne stiger, og kredsløbstæthederne stiger, har traditionelle mekaniske skæremetoder svært ved at opfylde de højpræcisions- og højeffektivitetskrav, der stilles til moderne halvlederproduktion. På grund af sine unikke fordele er laserskæring ved at blive den foretrukne løsning inden for disse områder.
Selvom laserskæringsteknologi stadig står over for udfordringer såsom høje udstyrsomkostninger og proceskompleksitet, gør dens unikke fordele inden for høj præcision og kontaktfri skader den til en vigtig retning for udviklingen inden for halvlederfremstilling. I takt med at laserteknologi og intelligente styresystemer fortsætter med at udvikle sig, forventes laserskæring yderligere at forbedre effektiviteten og kvaliteten af waferskæring, hvilket vil drive den fortsatte udvikling af halvlederindustrien.
2.3 Plasmaskæringsteknologi
Plasmaskæringsteknologi, som en fremadstormende wafer-udskæringsmetode, har fået betydelig opmærksomhed i de senere år. Denne teknologi bruger højenergiplasmastråler til præcist at skære wafere ved at kontrollere plasmastrålens energi, hastighed og skærebane og dermed opnå optimale skæreresultater.
Arbejdsprincip og fordele
Plasmaskæringsprocessen er afhængig af en højtemperatur- og højenergiplasmastråle, der genereres af udstyret. Denne stråle kan opvarme wafermaterialet til dets smelte- eller fordampningspunkt på meget kort tid, hvilket muliggør hurtig skæring. Sammenlignet med traditionel mekanisk skæring eller laserskæring er plasmaskæring hurtigere og producerer en mindre varmepåvirket zone, hvilket effektivt reducerer forekomsten af revner og skader under skæring.
I praktiske anvendelser er plasmaskæreteknologi særligt dygtig til håndtering af wafere med komplekse former. Dens højenergiske, justerbare plasmastråle kan nemt skære uregelmæssigt formede wafere med høj præcision. Derfor viser denne teknologi stort potentiale for udbredt anvendelse inden for mikroelektronikproduktion, især i specialfremstillet og småskalig produktion af high-end chips.
Udfordringer og begrænsninger
Trods de mange fordele ved plasmaskæringsteknologi står den også over for nogle udfordringer.
• Kompleks procesPlasmaskæringsprocessen er kompleks og kræver højpræcisionsudstyr og erfarne operatører for at sikrepræcision og stabilitet i skæring.
• Miljøkontrol og sikkerhedPlasmastrålens høje temperatur og høje energi kræver strenge miljøkontrol og sikkerhedsforanstaltninger, hvilket øger kompleksiteten og omkostningerne ved implementeringen.
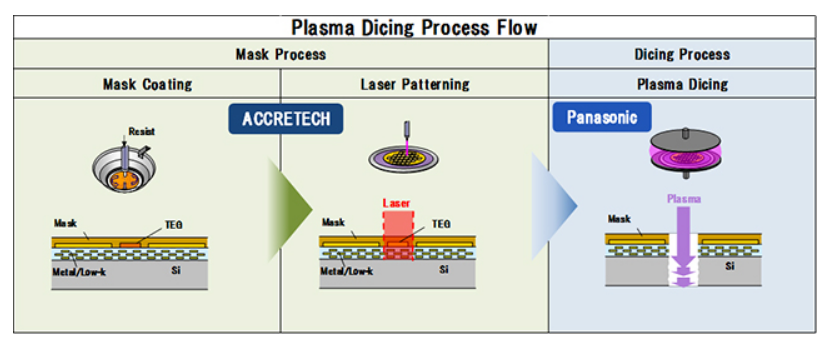
Fremtidige udviklingsretninger
Med teknologiske fremskridt forventes udfordringerne forbundet med plasmaskæring gradvist at blive overvundet. Ved at udvikle smartere og mere stabilt skæreudstyr kan afhængigheden af manuelle operationer reduceres, hvilket forbedrer produktionseffektiviteten. Samtidig vil optimering af procesparametre og skæremiljøet bidrage til at reducere sikkerhedsrisici og driftsomkostninger.
I halvlederindustrien er innovationer inden for waferskærings- og dicingteknologi afgørende for at drive industriens udvikling. Plasmaskæringsteknologi, med sin høje præcision, effektivitet og evne til at håndtere komplekse waferformer, er blevet en betydelig ny aktør på dette område. Selvom der stadig er nogle udfordringer, vil disse problemer gradvist blive løst med fortsat teknologisk innovation, hvilket vil bringe flere muligheder til halvlederproduktion.
Anvendelsesmulighederne for plasmaskæringsteknologi er enorme, og det forventes, at den vil spille en stadig vigtigere rolle i halvlederproduktion i fremtiden. Gennem kontinuerlig teknologisk innovation og optimering vil plasmaskæring ikke blot imødegå eksisterende udfordringer, men også blive en stærk drivkraft for halvlederindustriens vækst.
2.4 Skærekvalitet og påvirkende faktorer
Kvaliteten af waferskæring er afgørende for den efterfølgende spånpakning, testning og det endelige produkts samlede ydeevne og pålidelighed. Almindelige problemer, der opstår under skæring, omfatter revner, afskalning og skæreafvigelser. Disse problemer påvirkes af flere faktorer, der spiller sammen.
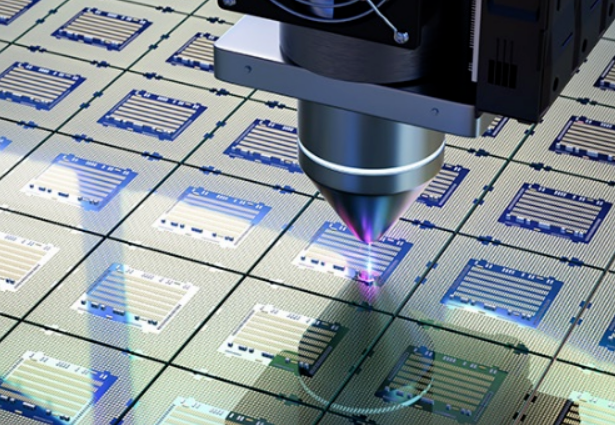
Kategori | Tilfreds | Indvirkning |
Procesparametre | Skærehastighed, tilspændingshastighed og skæredybde påvirker direkte stabiliteten og præcisionen af skæreprocessen. Forkerte indstillinger kan føre til spændingskoncentration og for stor varmepåvirket zone, hvilket resulterer i revner og afskalning. Det er vigtigt at justere parametrene korrekt baseret på wafermateriale, tykkelse og skærekrav for at opnå de ønskede skæreresultater. | De rigtige procesparametre sikrer præcis skæring og reducerer risikoen for defekter som revner og afskalning. |
Udstyrs- og materialefaktorer | -BladkvalitetBladets materiale, hårdhed og slidstyrke påvirker skæreprocessens glathed og skærefladens planhed. Blade af dårlig kvalitet øger friktion og termisk belastning, hvilket potentielt kan føre til revner eller afskalning. Det er afgørende at vælge det rigtige bladmateriale. -KølevæskeydelseKølevæsker hjælper med at reducere skæretemperaturen, minimere friktion og fjerne snavs. Ineffektiv kølevæske kan føre til høje temperaturer og ophobning af snavs, hvilket påvirker skærekvaliteten og effektiviteten. Det er afgørende at vælge effektive og miljøvenlige kølevæsker. | Klingekvaliteten påvirker snittets præcision og glathed. Ineffektiv kølevæske kan resultere i dårlig skærekvalitet og effektivitet, hvilket understreger behovet for optimal brug af kølevæske. |
Proceskontrol og kvalitetsinspektion | -ProceskontrolOvervågning og justering af vigtige skæreparametre i realtid for at sikre stabilitet og ensartethed i skæreprocessen. -KvalitetsinspektionKontrol af udseende efter skæring, dimensionsmålinger og test af elektrisk ydeevne hjælper med at identificere og løse kvalitetsproblemer hurtigt, hvilket forbedrer skærenøjagtigheden og ensartetheden. | Korrekt proceskontrol og kvalitetsinspektion er med til at sikre ensartede skæreresultater af høj kvalitet og tidlig opdagelse af potentielle problemer. |

Forbedring af skærekvaliteten
Forbedring af skærekvaliteten kræver en omfattende tilgang, der tager højde for procesparametre, udstyrs- og materialevalg, proceskontrol og inspektion. Ved løbende at forfine skæreteknologier og optimere procesmetoder kan præcisionen og stabiliteten af waferskæring forbedres yderligere, hvilket giver mere pålidelig teknisk support til halvlederindustrien.
#03 Håndtering og testning efter skæring
3.1 Rengøring og tørring
Rengørings- og tørretrinnene efter waferskæring er afgørende for at sikre chipskvaliteten og en problemfri udvikling af de efterfølgende processer. I denne fase er det vigtigt grundigt at fjerne siliciumrester, kølemiddelrester og andre forurenende stoffer, der genereres under skæringen. Det er lige så vigtigt at sikre, at chipsene ikke beskadiges under rengøringsprocessen, og efter tørring skal det sikres, at der ikke er fugt tilbage på chipsoverfladen for at forhindre problemer som korrosion eller elektrostatisk afladning.
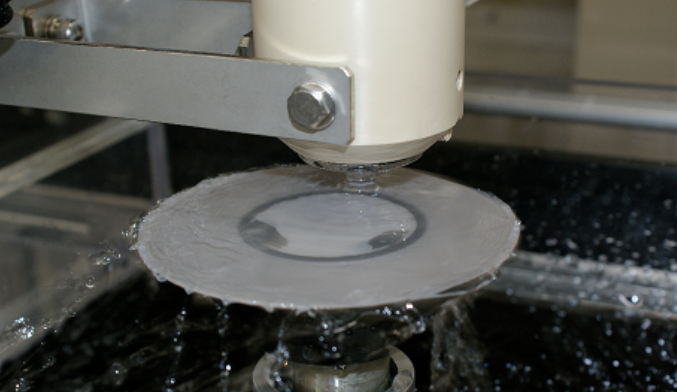
Håndtering efter opskæring: Rengørings- og tørringsproces
Procestrin | Tilfreds | Indvirkning |
Rengøringsproces | -MetodeBrug specialiserede rengøringsmidler og rent vand kombineret med ultralyds- eller mekaniske børsteteknikker til rengøring. | Sikrer grundig fjernelse af forurenende stoffer og forhindrer beskadigelse af spånerne under rengøring. |
-Valg af rengøringsmiddelVælg baseret på wafermateriale og forureningstype for at sikre effektiv rengøring uden at beskadige chippen. | Det rette valg af rengøringsmiddel er nøglen til effektiv rengøring og beskyttelse mod spåner. | |
-ParameterkontrolKontrollér nøje rengøringstemperatur, -tid og -koncentration af rengøringsopløsningen for at forhindre kvalitetsproblemer forårsaget af forkert rengøring. | Kontroller hjælper med at undgå at beskadige waferen eller efterlade forurenende stoffer, hvilket sikrer ensartet kvalitet. | |
Tørringsproces | -Traditionelle metoderNaturlig lufttørring og varmlufttørring, som har lav effektivitet og kan føre til opbygning af statisk elektricitet. | Kan resultere i langsommere tørretider og potentielle problemer med statisk elektricitet. |
-Moderne teknologierBrug avancerede teknologier såsom vakuumtørring og infrarød tørring for at sikre, at spånerne tørrer hurtigt og undgår skadelige virkninger. | Hurtigere og mere effektiv tørreproces, hvilket reducerer risikoen for statisk elektricitet eller fugtrelaterede problemer. | |
Udvalg og vedligeholdelse af udstyr | -Udvalg af udstyrHøjtydende rengørings- og tørremaskiner forbedrer proceseffektiviteten og kontrollerer potentielle problemer under håndteringen præcist. | Maskiner af høj kvalitet sikrer bedre forarbejdning og reducerer sandsynligheden for fejl under rengøring og tørring. |
-Vedligeholdelse af udstyrRegelmæssig inspektion og vedligeholdelse af udstyr sikrer, at det forbliver i optimal driftstilstand og garanterer spånkvaliteten. | Korrekt vedligeholdelse forhindrer udstyrsfejl og sikrer pålidelig og højkvalitetsbehandling. |
Rengøring og tørring efter skæring
Rengørings- og tørretrinnene efter waferskæring er komplekse og delikate processer, der kræver omhyggelig overvejelse af flere faktorer for at sikre det endelige forarbejdningsresultat. Ved at bruge videnskabelige metoder og strenge procedurer er det muligt at sikre, at hver chip går ind i de efterfølgende paknings- og testfaser i optimal stand.
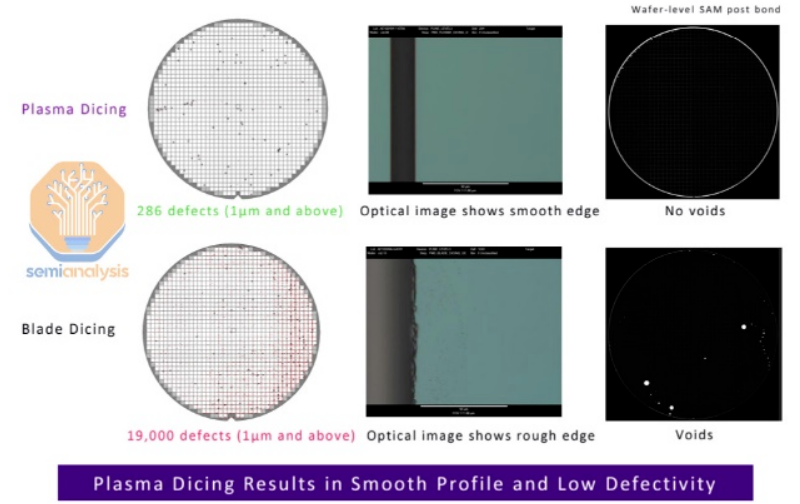
Inspektion og test efter skæring
Trin | Tilfreds | Indvirkning |
Inspektionstrin | 1.Visuel inspektionBrug visuelt eller automatiseret inspektionsudstyr til at kontrollere for synlige defekter som revner, afskalning eller kontaminering på spånoverfladen. Identificer hurtigt fysisk beskadigede spåner for at undgå spild. | Hjælper med at identificere og eliminere defekte spåner tidligt i processen, hvilket reducerer materialetab. |
2.StørrelsesmålingBrug præcisionsmåleinstrumenter til nøjagtigt at måle spåndimensioner, sikre at snitstørrelsen opfylder designspecifikationerne og forhindre ydelsesproblemer eller emballageproblemer. | Sikrer, at chipsene er inden for de krævede størrelsesgrænser, hvilket forhindrer forringelse af ydeevnen eller samlingsproblemer. | |
3.Elektrisk ydeevnetestningEvaluer vigtige elektriske parametre såsom modstand, kapacitans og induktans for at identificere ikke-kompatible chips og sikre, at kun ydeevnekvalificerede chips går videre til næste trin. | Sikrer, at kun funktionelle og ydeevnetestede chips bevæger sig videre i processen, hvilket reducerer risikoen for fejl i senere faser. | |
Testtrin | 1.Funktionel testningBekræft, at chippens grundlæggende funktionalitet fungerer som tilsigtet, og identificer og fjern chips med funktionelle abnormiteter. | Sikrer, at chips opfylder grundlæggende driftskrav, før de går videre til senere faser. |
2.PålidelighedstestEvaluer chips ydeevnestabilitet under langvarig brug eller barske miljøer, typisk involverende højtemperaturældning, lavtemperaturtestning og fugtighedstest for at simulere ekstreme forhold i den virkelige verden. | Sikrer, at chips kan fungere pålideligt under en række forskellige miljøforhold, hvilket forbedrer produktets levetid og stabilitet. | |
3.KompatibilitetstestBekræft, at chippen fungerer korrekt med andre komponenter eller systemer, og sørg for, at der ikke er fejl eller forringelse af ydeevnen på grund af inkompatibilitet. | Sikrer problemfri drift i virkelige applikationer ved at forhindre kompatibilitetsproblemer. |
3.3 Emballering og opbevaring
Efter waferskæring er chipsene et afgørende output i halvlederfremstillingsprocessen, og deres paknings- og opbevaringsfaser er lige så vigtige. Korrekt paknings- og opbevaringsforanstaltninger er afgørende, ikke kun for at sikre chipsenes sikkerhed og stabilitet under transport og opbevaring, men også for at yde stærk støtte til efterfølgende produktions-, test- og pakningsfaser.
Oversigt over inspektions- og testfaser:
Inspektions- og testtrinnene for chips efter waferskæring dækker en række aspekter, herunder visuel inspektion, størrelsesmåling, elektrisk ydeevnetest, funktionel test, pålidelighedstest og kompatibilitetstest. Disse trin er indbyrdes forbundne og komplementære og danner en solid barriere for at sikre produktkvalitet og pålidelighed. Gennem strenge inspektions- og testprocedurer kan potentielle problemer identificeres og løses hurtigt, hvilket sikrer, at det endelige produkt opfylder kundernes krav og forventninger.
Aspekt | Tilfreds |
Emballeringsforanstaltninger | 1.AntistatiskEmballagematerialer skal have fremragende antistatiske egenskaber for at forhindre statisk elektricitet i at beskadige enhederne eller påvirke deres ydeevne. |
2.FugttætEmballagematerialer skal have god fugtbestandighed for at forhindre korrosion og forringelse af den elektriske ydeevne forårsaget af fugtighed. | |
3.StødsikkerEmballagematerialerne skal give effektiv stødabsorbering for at beskytte chipsene mod vibrationer og stød under transport. | |
Lagringsmiljø | 1.FugtighedskontrolKontrollér nøje luftfugtigheden inden for et passende område for at forhindre fugtabsorption og korrosion forårsaget af for høj luftfugtighed eller statiske problemer forårsaget af lav luftfugtighed. |
2.RenhedOpbevar et rent opbevaringsmiljø for at undgå forurening af spåner med støv og urenheder. | |
3.TemperaturkontrolIndstil et rimeligt temperaturinterval og oprethold temperaturstabilitet for at forhindre accelereret ældning på grund af for høj varme eller kondensproblemer forårsaget af lave temperaturer. | |
Regelmæssig inspektion | Inspicer og evaluer regelmæssigt opbevarede chips ved hjælp af visuelle inspektioner, størrelsesmålinger og elektriske ydeevnetests for at identificere og håndtere potentielle problemer rettidigt. Planlæg brugen af chips baseret på opbevaringstid og -forhold for at sikre, at de bruges i optimal stand. |
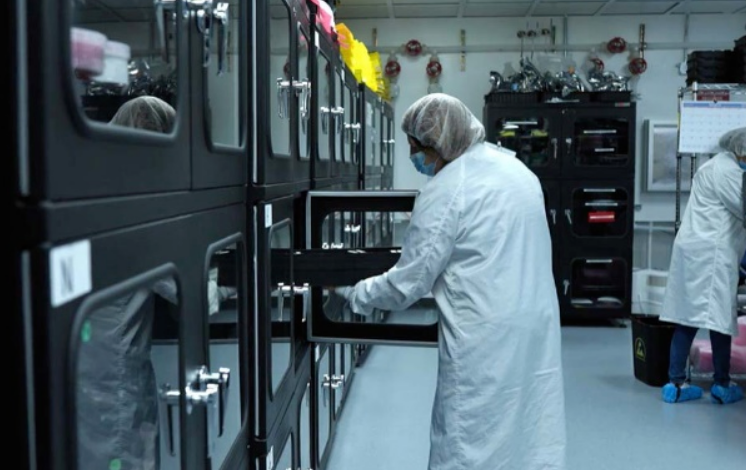
Problemet med mikrorevner og skader under wafer-udskæringsprocessen er en betydelig udfordring i halvlederfremstilling. Skærespændingen er den primære årsag til dette fænomen, da det skaber små revner og skader på waferoverfladen, hvilket fører til øgede produktionsomkostninger og et fald i produktkvaliteten.
For at imødegå denne udfordring er det afgørende at minimere skærebelastning og implementere optimerede skæreteknikker, værktøjer og forhold. Omhyggelig opmærksomhed på faktorer som bladmateriale, skærehastighed, tryk og kølemetoder kan bidrage til at reducere dannelsen af mikrorevner og forbedre processens samlede udbytte. Derudover undersøger løbende forskning i mere avancerede skæreteknologier, såsom laserskæring, måder at afbøde disse problemer yderligere.
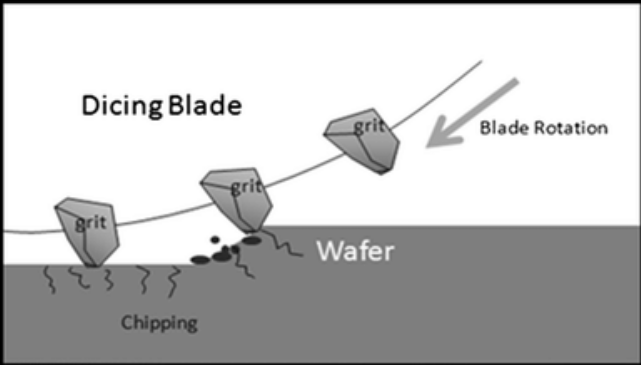
Da wafere er et skrøbeligt materiale, er de tilbøjelige til interne strukturelle ændringer, når de udsættes for mekanisk, termisk eller kemisk belastning, hvilket fører til dannelse af mikrorevner. Selvom disse revner måske ikke er umiddelbart synlige, kan de udvide sig og forårsage mere alvorlig skade, efterhånden som fremstillingsprocessen skrider frem. Dette problem bliver især problematisk under efterfølgende paknings- og testfaser, hvor temperaturudsving og yderligere mekaniske belastninger kan få disse mikrorevner til at udvikle sig til synlige brud, hvilket potentielt kan føre til chipfejl.
For at mindske denne risiko er det vigtigt at kontrollere skæreprocessen omhyggeligt ved at optimere parametre som skærehastighed, tryk og temperatur. Brug af mindre aggressive skæremetoder, såsom laserskæring, kan reducere den mekaniske belastning på waferen og minimere dannelsen af mikrorevner. Derudover kan implementering af avancerede inspektionsmetoder som infrarød scanning eller røntgenbilleddannelse under waferskæringsprocessen hjælpe med at opdage disse tidlige revner, før de forårsager yderligere skade.
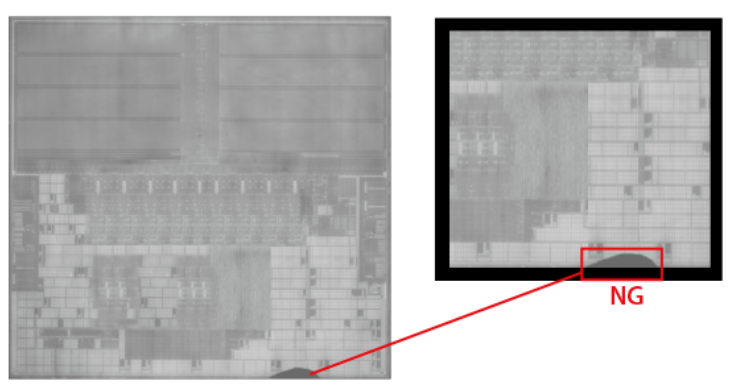
Skader på waferoverfladen er et væsentligt problem i udskæringsprocessen, da det kan have en direkte indvirkning på chippens ydeevne og pålidelighed. Sådanne skader kan være forårsaget af forkert brug af skæreværktøjer, forkerte skæreparametre eller materialefejl, der er iboende i selve waferen. Uanset årsagen kan disse skader føre til ændringer i kredsløbets elektriske modstand eller kapacitans, hvilket påvirker den samlede ydeevne.
For at løse disse problemer undersøges to nøglestrategier:
1. Optimering af skæreværktøjer og parametreVed at bruge skarpere klinger, justere skærehastigheden og ændre skæredybden kan spændingskoncentrationen under skæreprocessen minimeres, hvilket reducerer risikoen for skader.
2. Udforskning af nye skæreteknologierAvancerede teknikker som laserskæring og plasmaskæring giver forbedret præcision, samtidig med at de potentielt reducerer omfanget af skader på waferen. Disse teknologier undersøges for at finde måder at opnå høj skærenøjagtighed, samtidig med at termisk og mekanisk belastning på waferen minimeres.
Termisk påvirkningsområde og dets virkninger på ydeevne
I termiske skæreprocesser som laser- og plasmaskæring skaber høje temperaturer uundgåeligt en termisk stødzone på waferens overflade. Dette område, hvor temperaturgradienten er betydelig, kan ændre materialets egenskaber og dermed påvirke chippens endelige ydeevne.
Virkning af den termisk berørte zone (TAZ):
Ændringer i krystalstrukturenUnder høje temperaturer kan atomer i wafermaterialet omarrangere sig, hvilket forårsager forvrængninger i krystalstrukturen. Denne forvrængning svækker materialet og reducerer dets mekaniske styrke og stabilitet, hvilket øger risikoen for chipfejl under brug.
Ændringer i elektriske egenskaberHøje temperaturer kan ændre koncentrationen og mobiliteten af bærere i halvledermaterialer, hvilket påvirker chippens elektriske ledningsevne og strømtransmissionseffektivitet. Disse ændringer kan føre til en forringelse af chippens ydeevne, hvilket potentielt gør den uegnet til det tilsigtede formål.
For at afbøde disse effekter er kontrol af temperaturen under skæring, optimering af skæreparametrene og udforskning af metoder som køledyser eller efterbehandlinger vigtige strategier for at reducere omfanget af den termiske påvirkning og opretholde materialets integritet.
Samlet set er både mikrorevner og termiske stødzoner afgørende udfordringer inden for wafer-dicingteknologi. Fortsat forskning, sammen med teknologiske fremskridt og kvalitetskontrolforanstaltninger, vil være nødvendig for at forbedre kvaliteten af halvlederprodukter og styrke deres konkurrenceevne på markedet.
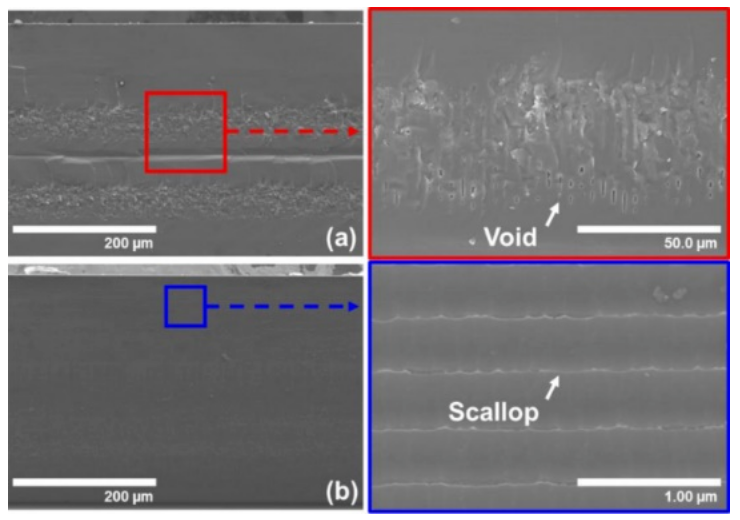
Foranstaltninger til kontrol af den termiske påvirkningszone:
Optimering af skæreprocesparametreReduktion af skærehastighed og -effekt kan effektivt minimere størrelsen af den termiske stødzone (TAZ). Dette hjælper med at kontrollere mængden af varme, der genereres under skæreprocessen, hvilket direkte påvirker waferens materialeegenskaber.
Avancerede køleteknologierAnvendelsen af teknologier som køling med flydende nitrogen og mikrofluidisk køling kan begrænse den termiske påvirkningszones rækkevidde betydeligt. Disse kølemetoder hjælper med at aflede varme mere effektivt, hvilket bevarer waferens materialeegenskaber og minimerer termisk skade.
MaterialevalgForskere udforsker nye materialer, såsom kulstofnanorør og grafen, som har fremragende varmeledningsevne og mekanisk styrke. Disse materialer kan reducere den termiske stødzone og samtidig forbedre chipsens samlede ydeevne.
Kort sagt, selvom den termiske stødzone er en uundgåelig konsekvens af termiske skæreteknologier, kan den effektivt kontrolleres gennem optimerede forarbejdningsteknikker og materialevalg. Fremtidig forskning vil sandsynligvis fokusere på finjustering og automatisering af termiske skæreprocesser for at opnå mere effektiv og præcis wafer-dicing.

Balancestrategi:
At opnå den optimale balance mellem waferudbytte og produktionseffektivitet er en konstant udfordring inden for wafer-dicingteknologi. Producenter skal overveje flere faktorer, såsom markedsefterspørgsel, produktionsomkostninger og produktkvalitet, for at udvikle en rationel produktionsstrategi og procesparametre. Samtidig er introduktion af avanceret skæreudstyr, forbedring af operatørfærdigheder og forbedret kontrol af råmaterialekvaliteten afgørende for at opretholde eller endda forbedre udbyttet, samtidig med at produktionseffektiviteten øges.
Fremtidige udfordringer og muligheder:
Med fremskridtene inden for halvlederteknologi står waferskæring over for nye udfordringer og muligheder. Efterhånden som chipstørrelserne krymper, og integrationen øges, vokser kravene til skærepræcision og -kvalitet betydeligt. Samtidig giver nye teknologier nye ideer til udvikling af waferskæringsteknikker. Producenter skal være opmærksomme på markedsdynamikken og teknologiske tendenser og løbende justere og optimere produktionsstrategier og procesparametre for at imødekomme markedsændringer og teknologiske krav.
Afslutningsvis kan producenterne ved at integrere overvejelser om markedsefterspørgsel, produktionsomkostninger og produktkvalitet, og ved at introducere avanceret udstyr og teknologi, forbedre operatørernes færdigheder og styrke råvarekontrollen, opnå den bedste balance mellem waferudbytte og produktionseffektivitet under waferdicing, hvilket fører til effektiv og højkvalitetsproduktion af halvlederprodukter.
Fremtidsudsigter:
Med hurtige teknologiske fremskridt udvikler halvlederteknologien sig i et hidtil uset tempo. Som et kritisk skridt i halvlederproduktion er waferskæreteknologi klar til spændende nye udviklinger. Fremadrettet forventes waferskæreteknologi at opnå betydelige forbedringer i præcision, effektivitet og omkostninger, hvilket vil tilføre ny vitalitet til den fortsatte vækst i halvlederindustrien.
Øget præcision:
I jagten på højere præcision vil waferskæreteknologien konstant flytte grænserne for eksisterende processer. Ved at studere de fysiske og kemiske mekanismer i skæreprocessen i dybden og præcist kontrollere skæreparametre, vil der opnås finere skæreresultater for at imødekomme stadig mere komplekse krav til kredsløbsdesign. Derudover vil udforskningen af nye materialer og skæremetoder forbedre udbytte og kvalitet betydeligt.
Forbedring af effektiviteten:
Nyt waferskæreudstyr vil fokusere på intelligent og automatiseret design. Introduktionen af avancerede styresystemer og algoritmer vil gøre det muligt for udstyret automatisk at justere skæreparametre for at imødekomme forskellige materialer og designkrav, hvilket vil forbedre produktionseffektiviteten betydeligt. Innovationer som multi-wafer-skæreteknologi og systemer til hurtig bladudskiftning vil spille en afgørende rolle i at forbedre effektiviteten.
Reduktion af omkostninger:
Omkostningsreduktion er en central retning for udviklingen af waferskæreteknologi. Efterhånden som nye materialer og skæremetoder udvikles, forventes udstyrsomkostninger og vedligeholdelsesudgifter at blive effektivt kontrolleret. Derudover vil optimering af produktionsprocesser og reduktion af skrotmængder yderligere reducere spild under fremstillingen, hvilket fører til et fald i de samlede produktionsomkostninger.
Smart produktion og IoT:
Integrationen af smart produktion og Internet of Things (IoT)-teknologier vil medføre transformative ændringer inden for waferskæringsteknologi. Gennem sammenkobling og datadeling mellem enheder kan hvert trin i produktionsprocessen overvåges og optimeres i realtid. Dette forbedrer ikke kun produktionseffektiviteten og produktkvaliteten, men giver også virksomheder mere præcise markedsprognoser og beslutningsstøtte.
I fremtiden vil waferskæringsteknologi gøre bemærkelsesværdige fremskridt inden for præcision, effektivitet og omkostninger. Disse fremskridt vil drive den fortsatte udvikling af halvlederindustrien og bringe flere teknologiske innovationer og bekvemmeligheder til det menneskelige samfund.
Opslagstidspunkt: 19. november 2024